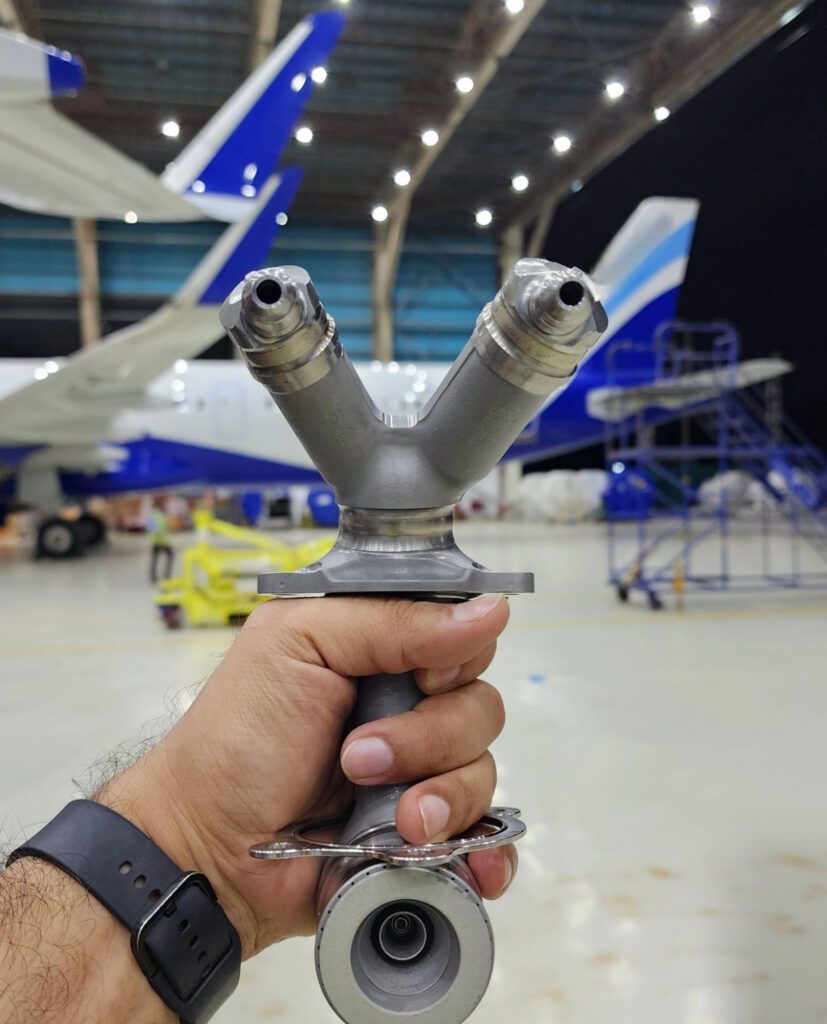
The CFM LEAP 1X engine is truly a next-generation engine in many respects. Among its numerous advanced features, the most notable is its second-generation Twin-Annular Pre-mixing Swirler combustor (TAPS II).
TAPS II is utilized in the CFM LEAP-1A engine for the Airbus A320neo family, the LEAP-1B engine for the Boeing 737 MAX, and the LEAP-1C engine for the COMAC C919.
The fuel nozzles of the CFM LEAP-1X engine are 3D-printed metal components, which are up to 25% lighter than traditional nozzles. TAPS II contributes to a significant reduction in the emissions of all four regulated pollutants compared to its predecessor, the CFM56 engine. The CFM LEAP engine family also offers 15-20% lower fuel consumption and CO2 emissions, along with a considerable improvement in noise levels compared to earlier generation engines.
However, in-service experience has revealed a major ‘coking’ issue with the engine’s state-of-the-art 3D-printed fuel nozzles, creating operational challenges for operators worldwide. Coking occurs due to environmental factors and engine conditions, such as the engineβs temperature at shutdown. This issue is not specific to the nozzle design but is caused by the evaporation of unburned fuel, which leads to the formation of hard carbon deposits in certain parts of the engine, particularly the fuel nozzles that spray fuel into the combustor.
This coking problem forced operators to replace fuel nozzles prematurely, sometimes even earlier than 1,200 hours, causing operational disruptions due to extended ground time for maintenance.
Recently, CFM International (CFM) introduced the LEAP-1A engine with a new RBS (Reverse Bleed System), designed to mitigate carbon build-up on fuel nozzles. The new system was certified by the Federal Aviation Administration and EASA – European Union Aviation Safety Agency in 2023. As a result, the need for on-wing fuel nozzle replacements and the associated maintenance burden will be significantly reduced and nozzle replacement will only be required at Shop visit.
New LEAP-1A engines began shipping with line-fit RBS systems in early 2024.Whereas in-service engines can be opted for retrofitting through implementation of few SBs to obtain the benefits of RBS functions.
A similar system is under development for the LEAP-1B, which is expected to be available in 2025. Early testing of the GE9X engine, which powers the Boeing 777-9, revealed signs of coking, leading GE to incorporate an RBS into its newest widebody turbofan engine. GE and Safran are equal partners (50/50) in CFM International (CFM).
Author – Rahul Mishra (Fleet Engineer)