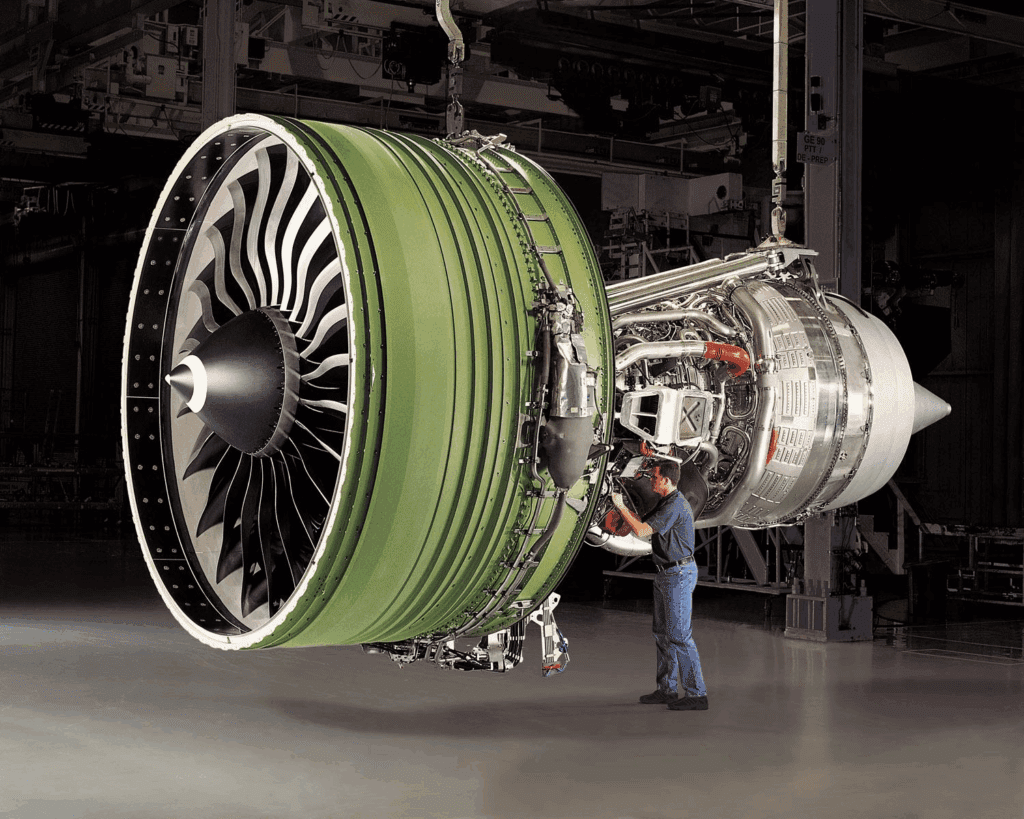
The GE90 engine, developed by General Electric Aviation, is a high-thrust turbofan engine specifically designed to power the Boeing 777 aircraft. Introduced in the mid-1990s, the GE90 has become notable for its unparalleled performance and reliability, particularly the GE90-115B variant, which is recognized as the most powerful commercial jet engine ever produced, capable of delivering up to 115,000 pounds of thrust. Its development marked a significant milestone in aviation engineering, emphasizing advancements in fuel efficiency, environmental sustainability, and innovative materials technology, including the use of carbon fiber composite fan blades that enhance performance while reducing weight and emissions.
The GE90’s operational history has been characterized by remarkable achievements, including record-setting flight tests and an impressive safety record, with a dispatch reliability rate exceeding 99.97% as of 2020.
Despite its success, the engine’s development was not without challenges. Early on, it faced concerns regarding its reliability and high operational costs, which led to significant engineering improvements.
Furthermore, in 2013, the Federal Aviation Administration (FAA) issued an Airworthiness Directive related to gearbox assembly failures that prompted critical safety inspections and updates.
The GE90 engine’s influence extends beyond its impressive specifications and reliability; it has played a crucial role in transforming long-haul aviation by allowing airlines to operate more efficiently on extended international routes, making it a preferred choice for operators of the Boeing 777 family. As the aviation industry evolves, the continued refinement of the GE90 engine and its technologies remains vital for meeting growing global demands for air travel and addressing regulatory standards for emissions and noise pollution.
Development
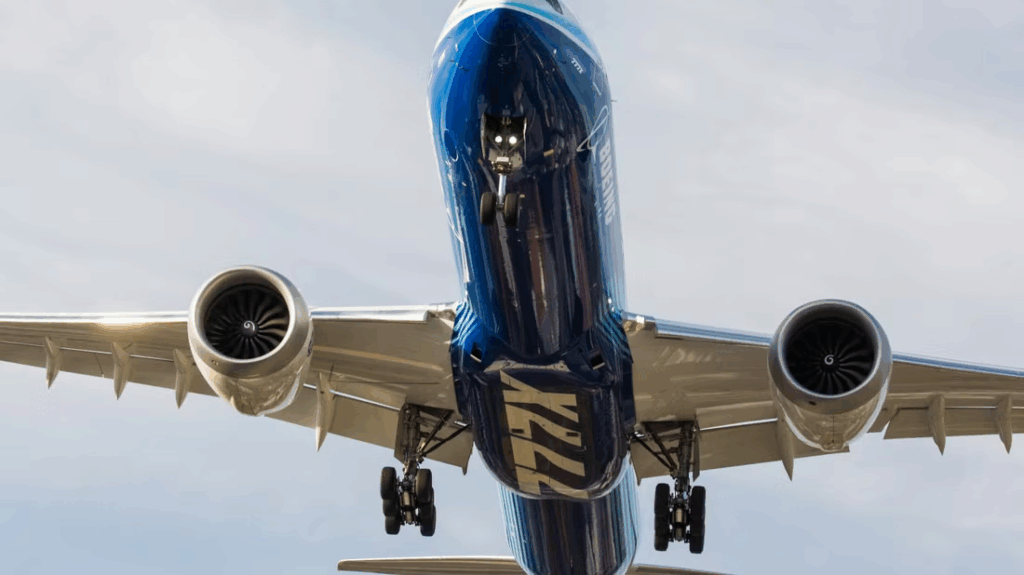
Key Milestones
Several crucial milestones highlight the progress of the GE90 engine’s development. The first major assembly of the Boeing 777, which the GE90 powers, began on January 4, 1993. Following comprehensive design and testing, the Boeing 777 received airworthiness certification on April 19, 1995, and the first unit was delivered to United Airlines on May 15, 1995. These dates not only marked the entry of a new aircraft model into the market but also underscored the successful collaboration between Boeing and GE. The GE90-115B variant, known for being one of the most powerful jet engines in the world, was part of this development process. It achieved notable design advancements, such as incorporating a 3-D-printed component in 2015, making it the first commercial engine to do so. Additionally, by June 2001, the engine was on schedule for its first full testing phase, demonstrating the project’s adherence to timelines and technical objectives.
Overview
The development of the GE90 engine began in January 1990 when General Electric announced its commitment to creating a high-thrust turbofan engine for the Boeing 777. The project marked a significant milestone in aviation engineering, focusing on efficiency and performance. The first full-scale engine core underwent testing in November 1992, leading to the first complete engine following a rigorous design and validation process
Design Solutions and Features
Throughout its development, the GE90 engine underwent numerous design iterations to enhance its efficiency and reduce its environmental impact. This included full engine analyses aimed at optimizing code development and design solutions.
The engine’s unique architecture, combined with its advanced materials and manufacturing techniques, contributed to improved fuel efficiency and reduced emissions, setting a new standard in commercial aviation propulsion technology
Future Directions
As the aviation industry evolves, so too does the GE90 engine’s development trajectory. Ongoing analysis and testing are critical for addressing airworthiness issues and improving engine reliability. Furthermore, continuous advancements in technology suggest that future iterations of the GE90 may further enhance performance while maintaining compliance with stringent regulatory requirements.
Technical Specifications
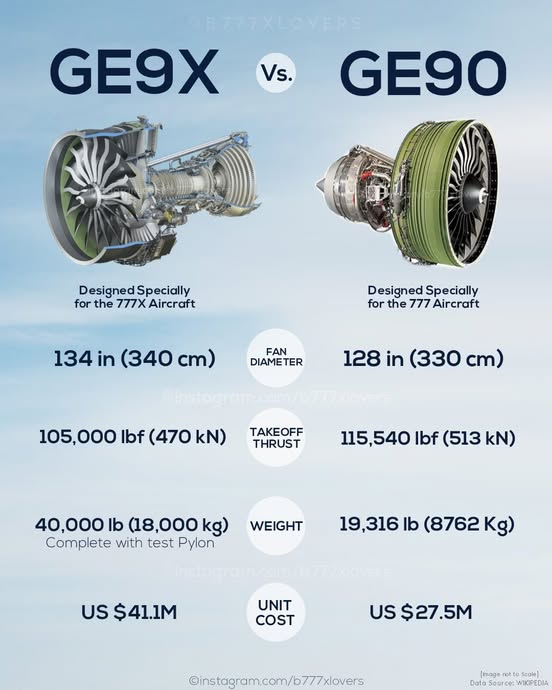
Engine Characteristics
The GE90 engine, designed and manufactured by GE Aviation, is renowned for being one of the most powerful jet engines in the world. Among its notable features, the engine boasts a fuel consumption rate that is approximately 10 percent better than large commercial turbofans from the pre-1995 generation. The engine’s configuration and operating intervals are defined in the GE90 Engine Manual, which details various operational settings and capabilities.
Design Innovations
A significant innovation in the GE90 engine is its use of 22 carbon fiber composite fan blades. This technology, which was first developed for the GE36 engine, offers double the strength at one-third the weight compared to traditional titanium fan blades, contributing to improved performance and fuel efficiency. The use of advanced materials extends to the engine’s construction, which incorporates high-temperature-resistant materials, including unique metal alloys and composites that enable the engine to withstand temperatures exceeding 3,000°F.
Cooling Technologies
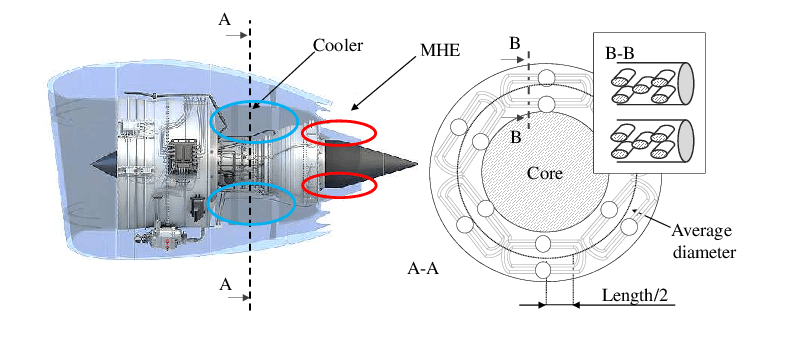
Efficient heat dissipation is critical for the GE90’s performance, as turbine components such as blades, vanes, nozzles, and shrouds must operate at optimal temperatures. Various cooling methods, including convection, impingement, and film cooling, are employed to maintain the temperature of these critical components, thus enhancing engine lifespan and reducing noise and emissions. Airlines typically operate the GE90 at lower-than-maximum thrust settings to further minimize maintenance and improve overall performance.
Performance Metrics
The GE90 engine’s bypass ratio refers to the mass of air bypassing the engine core during takeoff, while the overall pressure ratio denotes the pressure of the air exiting from the engine’s compressor compared to the air entering it. The engine’s design also accommodates increased loads and stresses through the use of a novel steel alloy, GE1014, for its fan shaft, which was necessary due to higher operational torque requirements.
Certification Achievements
In October 2003, a Boeing 777-300ER equipped with GE90-115B engines achieved a record for Extended-range Twin-engine Operational Performance Standards (ETOPS) by flying 330 minutes (five and a half hours) with one engine shut down, demonstrating the reliability and performance capabilities of the GE90 engine.
Applications
The GE90 engine, primarily developed for the Boeing 777, has played a pivotal role in the aircraft’s performance and operational efficiency. This powerful engine has been specifically designed to cater to the demanding requirements of long-haul flights, making it a preferred choice for airlines operating the Boeing 777 family.
Long-Haul Aviation
The GE90 engine is particularly well-suited for long-haul aviation due to its exceptional thrust capabilities and fuel efficiency. The Boeing 777-200ER, equipped with the GE90-94B variant, is known for its long-range capabilities, allowing airlines to operate on extended international routes without compromising performance. This is crucial in the context of a growing aviation market, especially in regions like Africa, where air traffic is expected to increase significantly over the coming decades.
Enhanced Capacity and Efficiency
In addition to its long-range applications, the GE90 engine also supports models like the Boeing 777-300ER, which features an extended fuselage that provides increased passenger capacity. This variant benefits from the engine’s reliability and efficiency, allowing airlines to maximize their operational performance while maintaining lower fuel costs. The advanced technology of the GE90 contributes to the overall efficiency of the Boeing 777, making it a favorite among airlines aiming for cost-effective operations.
Technological Advancements
The introduction of the GE90-115B engine marked a significant advancement in aviation technology, as it held the title of the most powerful commercial jet engine at the time. Its design incorporates innovative materials and engineering practices that enhance not only performance but also sustainability by reducing environmental impact. Airlines using the GE90 engines are thus positioned to meet increasing regulatory standards for emissions while still delivering high levels of service.
Future Prospects
As the aviation industry evolves, the GE90 engine continues to be an integral part of the Boeing 777’s family. The upcoming models, such as the 777X series, promise to build on the foundation laid by the GE90, incorporating even more advanced technologies that will enhance operational capabilities and fuel efficiency. The continued relevance of the GE90 engine underscores its crucial role in shaping the future of commercial aviation, ensuring that airlines can meet growing global demands effectively.
Innovations and Technology
The GE90 engine, developed by General Electric, represents a significant leap forward in jet engine technology, particularly in the context of commercial aviation. Its introduction marked a pivotal moment in the evolution of jet engines, which have become increasingly crucial for both military and commercial flight operations over the decades.
Advanced Materials

One of the hallmark innovations of the GE90 is its use of 22 carbon fiber composite fan blades, a technology that was first developed for the GE36 engine. These fan blades provide double the strength while weighing only one-third as much as traditional titanium blades, which contributes to improved efficiency and performance. The engine’s design includes swept rotor blades, which are the first of their kind in production engines, optimizing airflow and reducing drag during fligh.
Enhanced Performance
The GE90-115B variant is notable for being the most powerful commercial jet engine ever built, boasting record thrust levels that significantly enhance the operational efficiency of the Boeing 777. With a maximum nacelle diameter of 166 inches (4,200 mm), the GE90 engine incorporates advanced aerodynamics that play a crucial role in its overall performance. The combination of these features allows the GE90 to optimize fuel consumption, offering airlines better economic performance and a reduced environmental impact, aligning with the industry’s ongoing efforts to create more sustainable aviation solutions.
Design and Engineering
The design of the GE90 engine is a testament to innovative engineering, featuring a 33:1 pressure ratio achieved through a four-stage low-pressure compressor followed by a nine-stage high-pressure compressor. The engine’s power is delivered through a two-stage high-pressure turbine and a single-stage low-pressure turbine, which drive a four-stage free turbine. This complex arrangement maximizes efficiency while minimizing operational costs for airlines.
Operational History
The General Electric GE90 engine, which entered service in November 1995 with British Airways, has had a significant operational history characterized by numerous milestones and achievements. As one of the most powerful commercial aviation engines ever built, the GE90-115B variant boasts thrust ratings of up to 115,000 pounds-force, enabling exceptional performance on the Boeing 777 aircraft.
Notable Achievements
One of the engine’s most remarkable feats occurred during flight testing when the GE90-115B provided enough thrust to fly GE’s Boeing 747-100 testbed, N747GE, while the other three engines were at idle. This demonstration highlighted the immense power and capability of the GE90, solidifying its reputation in the aviation industry.
Engine Performance and Reliability
Throughout its operational life, the GE90 engine has demonstrated remarkable reliability. By November 2015, the fleet had accumulated over 50 million flight hours and more than 8 million cycles, showcasing its durability and efficiency. As of July 2020, the total hours flown by the fleet surpassed 100 million, with a dispatch reliability rate of 99.97%, reflecting its status as a trusted powerplant for airlines globally.
Technological Innovations
The GE90 engine has been recognized for its advanced technology, contributing to significant improvements in fuel efficiency and noise reduction. Airlines benefit from a fuel burn reduction of approximately 5-6% compared to previous engine models, alongside lower noise pollution levels, making it a preferred choice for long-haul operations. The engine’s design also allows for an in-flight shutdown rate (IFSD) of just one per million engine flight-hours, underscoring its operational safety.
Challenges and Issues
The development of the GE90 engine, which powers the Boeing 777, has encountered a series of significant challenges and issues over the years. These challenges have highlighted the complexities involved in creating an engine that meets modern aviation standards.
Technical Setbacks
The GE90 program faced numerous technical and financial setbacks, particularly in its early stages. Major airlines expressed concerns over the engine’s high costs and reliability, which posed risks for operators of the Boeing 777. These issues necessitated continuous improvements and innovative engineering solutions to ensure the engine’s competitiveness in the market.
Airworthiness Directives
In May 2013, the Federal Aviation Administration (FAA) issued an Airworthiness Directive (AD) concerning the GE90-110B1 and GE90-115B turbofan engines. This emergency directive was prompted by reports of failures in the transfer gearbox assemblies, leading to in-flight shutdowns (IFSDs). Investigations revealed that the failures were linked to cracking and separation of TGB radial gears, attributed to manufacturing processes and operational stresses. If unaddressed, these failures could result in further IFSDs, loss of thrust control, and potential damage to the aircraft. The directive mandated compliance within five days to replace all affected modules.
Incidents and Lessons Learned
Despite the overall strong safety record of the Boeing 777, there have been notable incidents that underscored the importance of engine reliability. One incident involved a United Airlines Boeing 777 making an emergency landing due to tire failure shortly after takeoff, emphasizing the necessity of rigorous maintenance and safety checks. Another critical incident involved a crash landing caused by engine failure, which reiterated the ongoing need for advancements in engine technology to enhance reliability.
Future Outlook
Looking ahead, the aviation market continues to show a strong demand for larger aircraft like the Boeing 777, driven by increasing passenger and cargo traffic, especially in emerging markets. As air traffic is projected to grow significantly in the coming decades, ongoing innovations and solutions to the challenges faced by the GE90 engine will be essential in maintaining its relevance and ensuring the safety and efficiency of the Boeing 777 in the future.
By – Aeropeep Team
#GE90 engine #Boeing 777 engine #GE90 engine specs #GE90 jet engine #most powerful jet engine #GE90 thrust #Boeing 777 propulsion system #GE90 engine diagram
#GE90 maintenance #Boeing 777 ETOPS engine #jet engine with FADEC GE90 vs Rolls-Royce #Trent twin-spool engine design #GE90 fan blade material #GE90 fuel efficiency #GE90 engine design
- The GE90 Engine: Powering the Boeing 777 with Precision
- The Future of Sustainable Aviation: How Aircraft Engineers Are Redesigning Flight for a Greener Tomorrow
- Hard Landing – The Airbus A321-271NX aircraft (N607FR)
- Shift Towards Electric and Hybrid Aircraft
- How Flightradar 24 Revolutionizes Flight Tracking and Safety